The Science Behind Porosity: A Comprehensive Overview for Welders and Fabricators
Understanding the complex systems behind porosity in welding is important for welders and makers striving for impressive workmanship. From the make-up of the base materials to the details of the welding process itself, a wide variety of variables conspire to either worsen or ease the existence of porosity.
Understanding Porosity in Welding
FIRST SENTENCE:
Evaluation of porosity in welding discloses essential insights into the honesty and high quality of the weld joint. Porosity, defined by the visibility of tooth cavities or spaces within the weld steel, is a typical concern in welding processes. These spaces, if not correctly addressed, can jeopardize the architectural stability and mechanical properties of the weld, resulting in prospective failures in the ended up product.
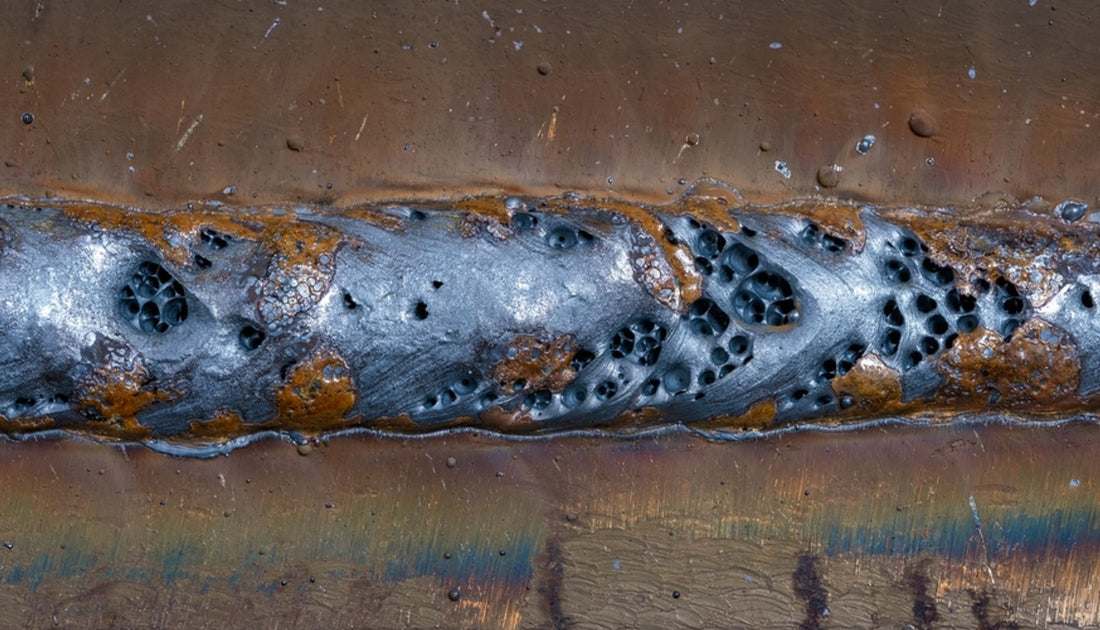
To discover and quantify porosity, non-destructive testing approaches such as ultrasonic testing or X-ray evaluation are often utilized. These techniques allow for the recognition of inner problems without compromising the honesty of the weld. By assessing the size, shape, and circulation of porosity within a weld, welders can make educated decisions to improve their welding procedures and attain sounder weld joints.

Aspects Influencing Porosity Formation
The occurrence of porosity in welding is affected by a myriad of variables, varying from gas protecting performance to the complexities of welding criterion settings. Welding specifications, consisting of voltage, current, travel rate, and electrode kind, additionally influence porosity formation. The welding technique employed, such as gas steel arc welding (GMAW) or protected steel arc welding (SMAW), can influence porosity formation due to variations in warm distribution and gas coverage - What is Porosity.
Results of Porosity on Weld Top Quality
Porosity development dramatically endangers the architectural stability and mechanical residential properties of bonded joints. When porosity exists in a weld, it produces voids or cavities within the material, minimizing the overall toughness of the joint. These spaces work as stress concentration factors, go to these guys making the weld more susceptible to cracking and failure under lots. The presence of porosity likewise deteriorates the weld's resistance to rust, as the trapped air or gases within the voids can respond with the surrounding setting, bring about degradation gradually. Furthermore, porosity can prevent the weld's capability to withstand pressure or effect, additional endangering the general high quality and dependability of the bonded framework. In crucial applications such as aerospace, vehicle, or structural constructions, where security and resilience are vital, the damaging impacts of porosity on weld top quality can have extreme repercussions, stressing the importance of reducing porosity via appropriate welding methods and treatments.
Strategies to Reduce Porosity
Furthermore, using the proper welding parameters, such as the correct voltage, present, and take a trip speed, is essential in protecting against porosity. Maintaining a consistent arc length and angle during welding additionally helps decrease the probability of porosity.

Utilizing the ideal welding technique, such as back-stepping or employing a weaving motion, can also aid distribute heat equally and decrease the opportunities of porosity formation. By carrying out these methods, welders can successfully reduce porosity and produce high-quality bonded joints.
Advanced Solutions for Porosity Control
Applying innovative modern technologies and innovative techniques plays a critical duty in achieving remarkable control over porosity in welding procedures. Furthermore, employing innovative welding techniques such as pulsed MIG welding or changed ambience welding can additionally help reduce porosity concerns.
Another innovative solution includes using sophisticated welding tools. As an example, utilizing devices with integrated attributes like waveform control and advanced source of power investigate this site can enhance important site weld quality and decrease porosity risks. The implementation of automated welding systems with precise control over parameters can considerably minimize porosity issues.
Furthermore, incorporating innovative monitoring and evaluation innovations such as real-time X-ray imaging or automated ultrasonic testing can help in finding porosity early in the welding procedure, permitting prompt rehabilitative activities. Generally, incorporating these sophisticated remedies can greatly improve porosity control and enhance the total top quality of bonded parts.
Verdict
In conclusion, recognizing the scientific research behind porosity in welding is vital for welders and makers to create high-grade welds - What is Porosity. Advanced remedies for porosity control can better boost the welding process and make certain a solid and trusted weld.